Share this
How to Take Your Ecommerce Warehouse Efficiency to the Next Level
by Shipfusion Team on May. 8, 2025
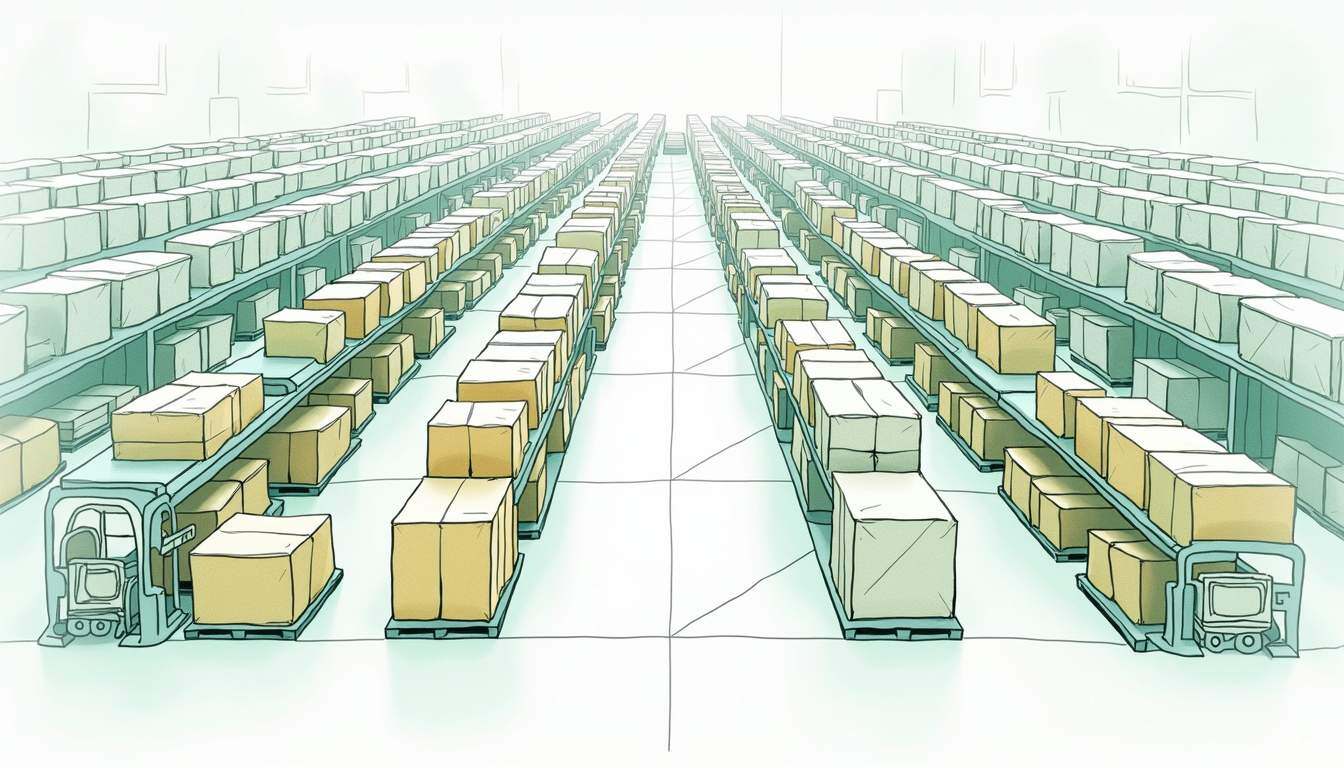
Ecommerce warehouse efficiency is about nailing that perfect mix of precision, space optimization, and the ability to scale without compromising service. To achieve it, all businesses, especially online stores experiencing rapid growth, need to evaluate their warehouse operations with a sharp lens. Below, we break down strategies to improve workflows, boost output, and reduce operational waste.
What Ecommerce Warehouse Efficiency Actually Means
Warehouse efficiency measures how effectively your operations turn inputs (labor, equipment, space) into outputs (fulfilled, error-free orders). It includes everything from receiving inventory and storing it properly to picking, packing, and shipping orders. Efficient warehouses minimize unnecessary movement, eliminate duplicate processes, and maintain high levels of order accuracy, all while keeping costs under control.
Efficiency isn’t one-size-fits-all. A brand shipping skincare products from three warehouses faces different challenges than a brand fulfilling custom subscription boxes from a single location. That’s why efficiency must be evaluated in context: SKU complexity, order volume, seasonal spikes, and fulfillment channels all shape what optimal looks like.
KPIs That Actually Reflect Ecommerce Warehouse Efficiency
Tracking the right data is essential for identifying bottlenecks and opportunities for improvement. Focus on supply chain KPIs that reflect speed, accuracy, and space use:
-
Order Accuracy Rate: This is your canary in the coal mine. High order accuracy reduces returns and improves customer satisfaction. A good benchmark is 99.9% or higher.
-
Inventory Turnover Ratio: Measures how often you sell and replace inventory within a timeframe. Low turnover could indicate overstocking or poor forecasting. High turnover with stockouts may suggest under-ordering or inefficient replenishment.
-
Pick and Pack Time per Order: Is your team spending 30 seconds or 3 minutes locating an item? Monitoring pick and pack time reveals layout and process issues that are otherwise easy to overlook.
-
Space Utilization Rate: If only 60% of your warehouse is used effectively, you’re paying for unused square footage. Efficient racking systems, vertical storage, and optimized slotting strategies can dramatically increase utilization.
WMS: The Backbone of Scalable Ecommerce Warehouse Efficiency
Warehouse Management Systems (WMS) go far beyond inventory tracking. A strong WMS reduces manual input, enforces fulfillment rules, and helps teams make smarter decisions based on real-time data.
Here’s what makes a WMS truly effective for ecommerce:
-
Channel-Agnostic Inventory Syncing: Inventory should update in real time across every sales channel, whether that’s Shopify, Amazon, or B2B EDI orders.
-
Rule-Based Order Routing: Automatically direct orders to the warehouse or fulfillment center best equipped to ship it fastest and cheapest.
-
Barcode Scanning & Lot Tracking: This ensures accuracy in every scan and is a must-have for brands with expiration dates, batch codes, or regulated products.
-
Analytics & Exception Reporting: Instead of waiting for customer complaints, exception reports alert you to mispicks, slow-moving items, or delayed shipments as they happen.
Physical Layout: Designing for Movement, Not Storage
Too often, warehouse layouts are built around what fits, not what flows. Optimizing the layout of your warehouse means thinking like a picker, not a planner.
-
High-Volume SKUs Up Front: Store your fastest movers closest to packing stations. This alone can shave hours off daily pick time in high-volume environments.
-
Logical Zone Designation: Group items by picking method (single vs. batch pick), weight, or category. It reduces walking time and errors.
-
Pick Paths That Avoid Congestion: Ensure pickers aren’t doubling back or crossing paths unnecessarily. Use data to establish the most efficient path between items.
-
Use Vertical Space Intentionally: Store slow-moving or overstock items higher up, keeping frequently picked products within easy reach.
Inventory Management as a Precision Tool
Inventory accuracy impacts more than just fulfillment – it affects forecasting, reordering, and customer satisfaction.
A few well-targeted practices go a long way:
-
ABC Inventory Classification: Group SKUs into A (high velocity), B (moderate), and C (low) categories. Apply different handling and audit strategies to each tier to balance accuracy with effort.
-
Cycle Counting vs. Annual Audits: Frequent cycle counts (daily or weekly spot checks) catch discrepancies early and prevent year-end surprises.
-
Just-in-Time Inventory, with Buffers: JIT works well for predictable items, but ecommerce brands should still build in buffers for seasonal items or high-growth SKUs to avoid stockouts.
Automation That’s Actually Worth the Investment
Automation isn’t about replacing workers – it’s about allowing your team to focus on tasks that require human judgment.
Start small and scale:
-
Conveyor Systems for Batch Picking: Reduce picker travel time and allow parallel workflows by moving totes or bins through stations.
-
Automated Labeling & Packing Machines: Especially valuable for high-volume DTC brands. Speeds up outbound processing and reduces labor costs.
-
Barcode & RFID Systems: These prevent mispicks and give real-time insights into inventory movement. RFID, while more costly, is ideal for high-value or regulated products.
-
Smart Replenishment Algorithms: These trigger POs or stock transfers based on real-time velocity, not static reorder points.
Workforce Optimization: People Drive Efficiency
No technology can fix a disengaged or undertrained team. People are the driving force behind every successful warehouse, and investing in them yields real returns.
-
Cross-Training: Teaching employees multiple roles – picking, packing, inventory – adds flexibility and reduces downtime when someone’s out or volume shifts.
-
Micro-Learning Modules: Short, focused training videos or on-floor coaching keep teams sharp without pulling them off the floor for hours.
-
Performance Dashboards: Transparency helps. Showing pick rates, error rates, or order volumes in real time can drive healthy competition and accountability.
-
Feedback Loops: Ask pickers and packers what slows them down. Often, frontline workers know the inefficiencies leadership can’t see.
A New Level of Ecommerce Warehouse Efficiency Awaits
At Shipfusion, streamlining your ecommerce warehouse efficiency is just the beginning. We understand the complexities of ecommerce fulfillment and are here to help you take your business to the next level with a comprehensive 3PL fulfillment services. Enjoy peace of mind knowing that your inventory is managed efficiently and your orders are shipped promptly and accurately.
Get pricing today and discover how Shipfusion can transform your fulfillment process and delight your customers.
Share this
You May Also Like
These Related Articles
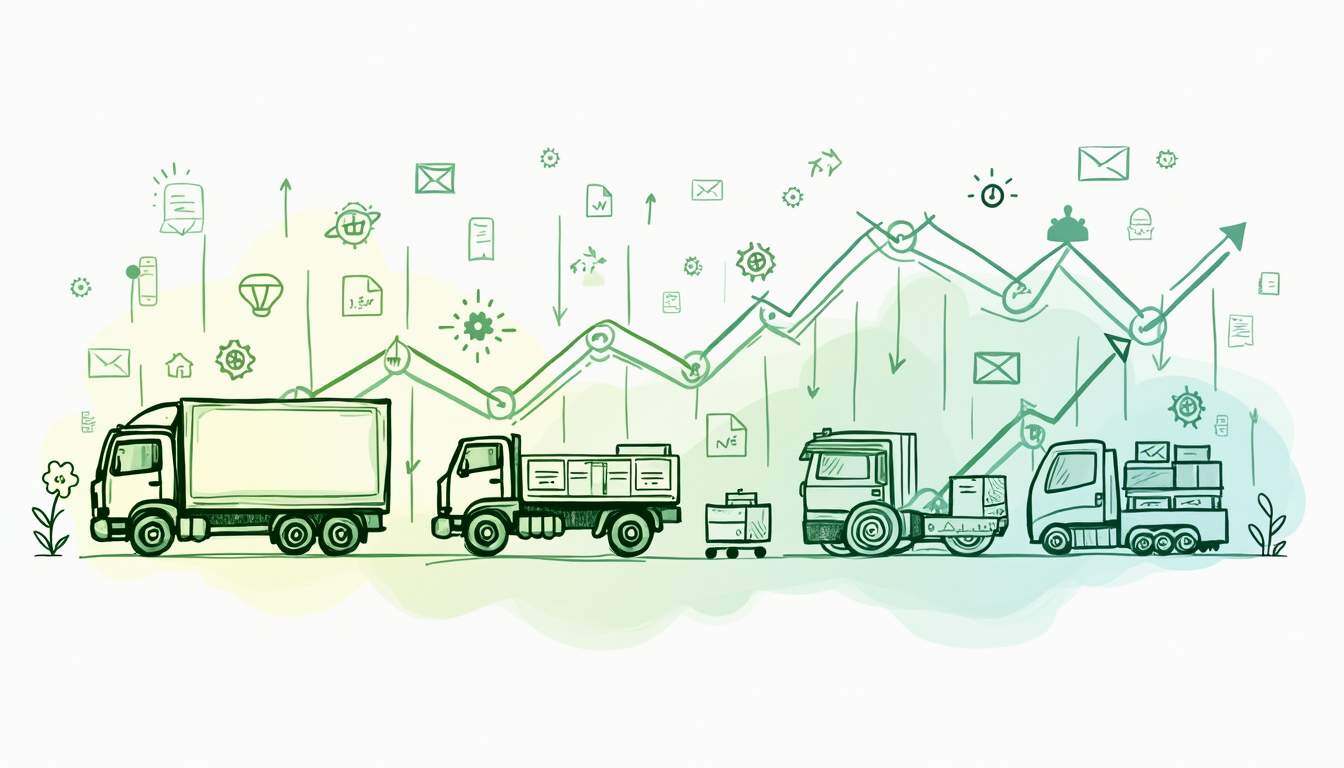
Ecommerce Fulfillment Cost Optimization Strategies You May Have Missed
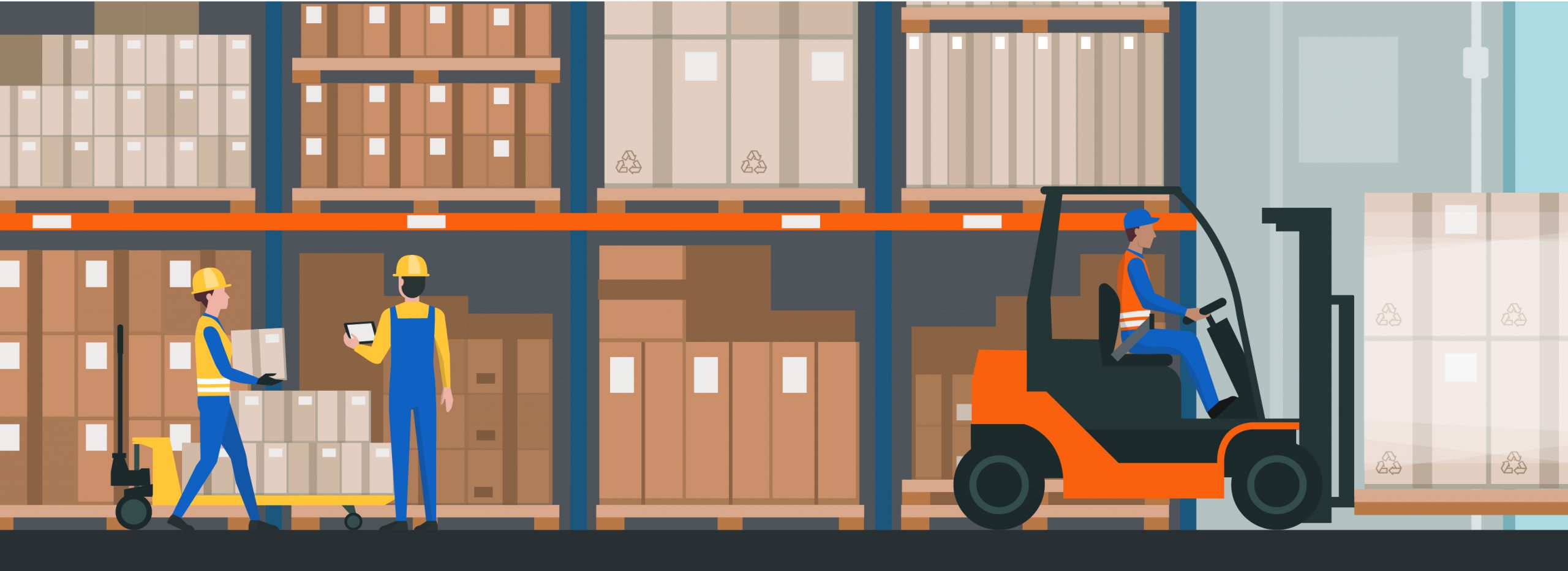
Best Ecommerce Warehousing Strategies for 2024
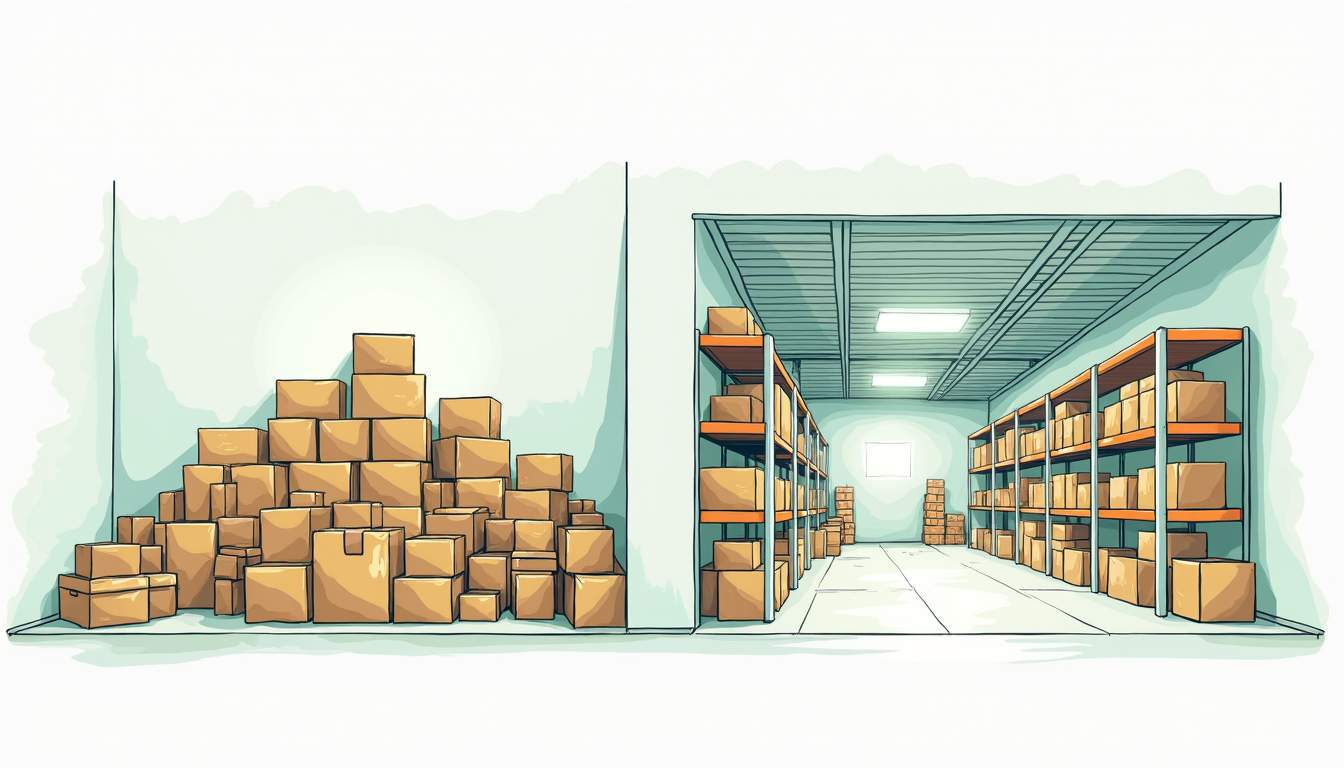
Cluttered Warehouse? Here are Some Solutions.
- August 2025 (4)
- July 2025 (16)
- June 2025 (22)
- May 2025 (27)
- April 2025 (27)
- March 2025 (26)
- February 2025 (26)
- January 2025 (34)
- December 2024 (16)
- November 2024 (22)
- October 2024 (22)
- September 2024 (27)
- August 2024 (9)
- July 2024 (8)
- June 2024 (5)
- May 2024 (8)
- April 2024 (7)
- March 2024 (6)
- February 2024 (6)
- January 2024 (5)
- December 2023 (3)
- November 2023 (3)
- October 2023 (5)
- September 2023 (4)
- August 2023 (2)
- July 2023 (1)
- June 2023 (4)
- March 2023 (2)
- October 2022 (1)
- September 2022 (5)
- August 2022 (4)
- July 2022 (7)
- June 2022 (4)
- May 2022 (4)
- April 2022 (6)
- March 2022 (2)
- February 2022 (1)
- January 2022 (3)
- December 2021 (2)
- November 2021 (4)
- October 2021 (2)
- September 2021 (5)
- August 2021 (4)
- July 2021 (4)
- June 2021 (3)
- May 2021 (2)
- April 2021 (3)
- March 2021 (3)
- February 2021 (3)
- January 2021 (2)
- December 2020 (4)
- November 2020 (2)
- October 2020 (4)
- September 2020 (2)
- July 2020 (5)
- June 2020 (4)
- May 2020 (2)
- April 2020 (2)
- March 2020 (4)
- February 2020 (1)
- December 2019 (1)
- May 2018 (1)
- March 2018 (2)
- February 2018 (3)
- January 2018 (3)
- November 2017 (3)
- July 2017 (4)
- March 2017 (3)
- February 2017 (5)
- January 2017 (3)
- December 2016 (4)
- November 2016 (6)
- October 2016 (6)
- October 2015 (1)
- September 2015 (1)
- June 2015 (3)
- May 2015 (3)
- August 2014 (1)
- July 2014 (1)
- March 2014 (1)
- February 2014 (1)